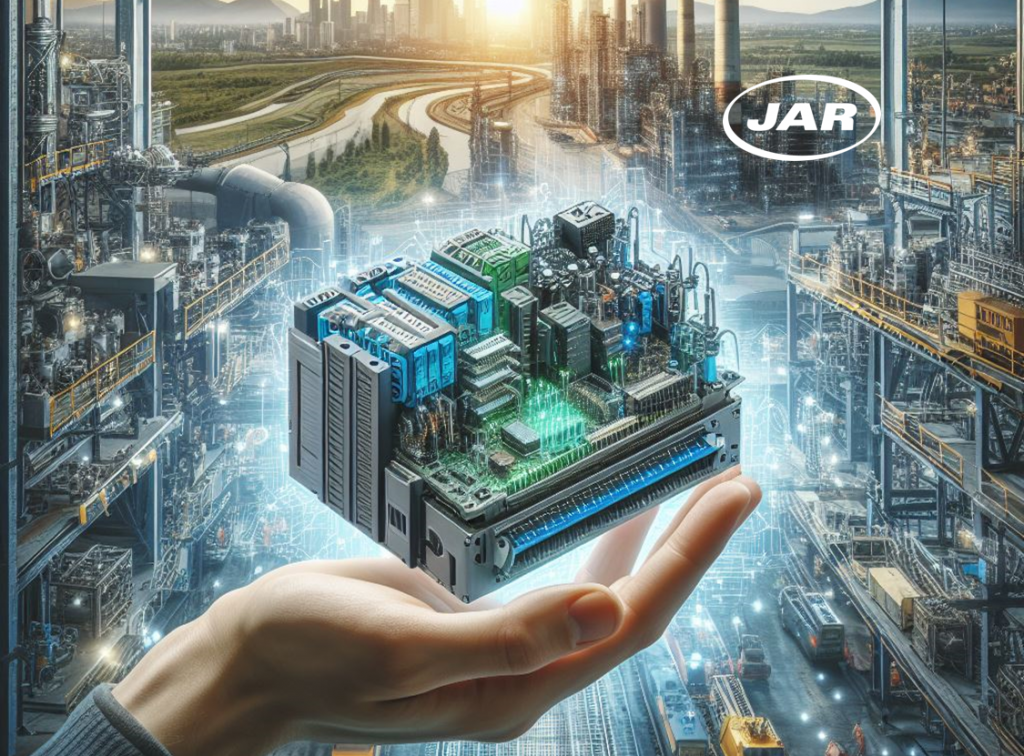
Introducción: Tendencias del mercado en las Tecnolgías Operativas (OT).
La industria de la automatización industrial está en constante evolución, impulsada por la necesidad de mejorar la eficiencia, la productividad y la seguridad en los procesos industriales. En este contexto, los Controladores Lógicos Programables (PLC) juegan un papel fundamental al proporcionar una solución flexible y confiable para controlar y supervisar una amplia gama de aplicaciones industriales. Unas de las marcas líderes en este campo son Modicon y Telemecanique, actualmente pertenecientes al portafolio de automatización de Schneider Electric y que han estado a la vanguardia de la innovación en PLCs, respondiendo a las demandas cambiantes del mercado.
Reseña de los PLC: Surgimiento, desarrollo e impacto en las revoluciones industriales.
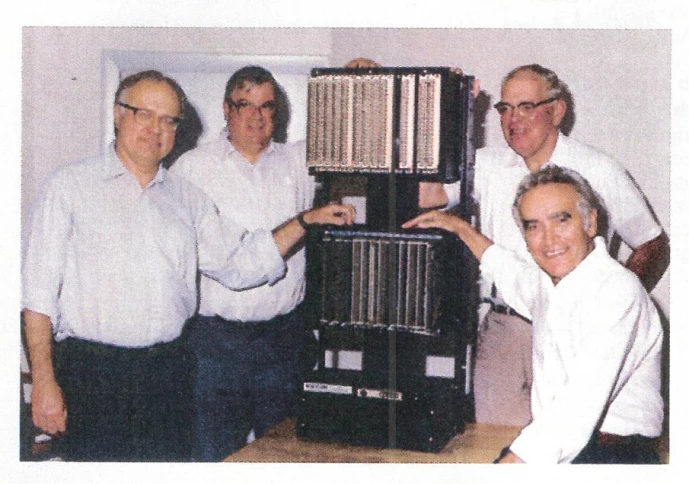
Los Controladores Lógicos Programables (PLC) surgieron en la década de 1960 como una alternativa a los sistemas de control cableados en la industria manufacturera. Su desarrollo extensivo se debió a la necesidad de una solución más flexible, que permitiera la reconfiguración rápida y la programación sencilla para adaptarse a diferentes procesos industriales. Su impacto ha sido significativo en la 3ra y la 4ta revolución industrial, al facilitar la automatización de procesos, mejorar la eficiencia y reducir los costos de producción.
Y… ¿Como funciona un PLC?
Funciona siguiendo un ciclo de escaneo continuo que incluye tres etapas principales:
- Lectura de entradas: El PLC lee el estado de las señales de entrada provenientes de sensores, interruptores u otros dispositivos conectados al sistema.
- Ejecución del programa: Basándose en el programa almacenado en su memoria, el PLC realiza una serie de cálculos y decisiones lógicas para determinar las acciones que deben tomarse en función de las entradas recibidas.
- Actualización de salidas: Una vez que se ha ejecutado el programa, el PLC actualiza el estado de las señales de salida, que controlan dispositivos como motores, válvulas o luces, según las decisiones tomadas en el paso anterior.
Este ciclo se repite continuamente a una velocidad predeterminada, lo que permite al PLC controlar eficientemente el proceso en tiempo real. El programa que guía el funcionamiento del PLC se crea utilizando software especializado y se carga en la memoria del PLC antes de su utilización. Esto permite una gran flexibilidad, ya que el programa puede modificarse fácilmente para adaptarse a diferentes requisitos de control.
Y… ¿Qué son las entradas y salidas en un PLC?
Los PLC pueden tener una variedad de tipos de entradas y salidas (E/S) que se utilizan para interactuar con el entorno y controlar dispositivos. Aquí tienes algunos ejemplos de los tipos más comunes:
- Entradas digitales:
- Ejemplo de uso: Interruptores de límite, sensores de proximidad, botones pulsadores.
- Utilización: Las entradas digitales detectan estados binarios, como abierto/cerrado o encendido/apagado. Se utilizan para detectar eventos o condiciones en el entorno y proporcionar información al PLC sobre el estado del proceso.
- Salidas digitales:
- Ejemplo de uso: Relés, contactores, solenoides.
- Utilización: Las salidas digitales permiten al PLC controlar dispositivos de conmutación, como motores, válvulas o luces. Cuando una salida digital se activa, envía una señal de encendido o apagado al dispositivo conectado, permitiendo al PLC controlar su funcionamiento.
- Entradas analógicas:
- Ejemplo: Sensores de temperatura, sensores de presión, transmisores de corriente, instrumentos de nivel.
- Utilización: Las entradas analógicas miden valores continuos, como temperatura, presión o nivel. Estas señales analógicas se convierten en valores digitales que el PLC puede procesar y utilizar para controlar el proceso de manera más precisa.
- Salidas analógicas:
- Ejemplo: Válvulas proporcionales, variadores de frecuencia, dispositivos de control de velocidad.
- Utilización: Las salidas analógicas generan señales de control proporcionales, permitiendo al PLC controlar dispositivos que requieren un ajuste continuo, como la velocidad o la posición.
Estos son solo algunos ejemplos de los tipos de entradas y salidas que se encuentran comúnmente en los PLC. La combinación específica de E/S utilizada en un PLC dependerá de los requisitos del proceso que se esté controlando.
Evolución tecnológica de los PLC hasta la actualidad
Desde su aparición, los PLC han experimentado una evolución tecnológica constante. Desde los primeros modelos basados en relés hasta los modernos PLC con capacidades de procesamiento avanzadas, la tecnología ha evolucionado para ofrecer mayor potencia de cálculo, capacidad de almacenamiento y funcionalidades de comunicación. Los avances recientes incluyen la integración de tecnologías como la conexión a bases de datos, el Internet de las Cosas (IoT) y la computación en la nube, que permiten la conectividad y la recopilación de datos en tiempo real.
Y… ¿Qué ha sucedido con las redes industriales?
La evolución de las redes industriales en los PLCs ha sido significativa a lo largo del tiempo, con avances en la velocidad de comunicación, la capacidad de integración y la interoperabilidad entre dispositivos. Por ejemplo el bus Modbus han desempeñado un papel importante en esta evolución:
- Modbus:
- Modbus se originó en las primeras etapas del uso de PLCs, principalmente en las décadas de 1970 y 1980.
- Este protocolo fue ampliamente adoptado debido a su simplicidad y facilidad de implementación en conexiones seriales como RS-232 y RS-485.
- Modbus Plus:
- Modbus Plus es una extensión del protocolo Modbus que se desarrolló para operar en redes de área local con un bus de alta velocidad.
- Este avance tuvo lugar en la década de 1980 y permitió una comunicación más rápida y eficiente en comparación con Modbus RTU.
- Modbus TCP:
- Modbus TCP es una versión del protocolo Modbus diseñada para operar sobre TCP/IP, el protocolo fundamental de Internet.
- Su desarrollo y adopción tuvieron lugar en las últimas décadas del siglo XX, y se consolidó como una solución de red industrial eficiente y adaptada a entornos basados en Ethernet.
En resumen, la evolución de las redes industriales en los PLCs, desde Modbus hasta Modbus TCP, ha estado marcada por mejoras en la velocidad, la capacidad de integración y la interoperabilidad, lo que ha permitido un mejor rendimiento y una mayor flexibilidad en una variedad de aplicaciones industriales.
Evolución de los lenguajes de programación
Los primeros PLC utilizaban lenguajes de programación propietarios, como el LL984. Sin embargo, la estandarización fue impulsada por la norma IEC 61131.
La programación según la norma IEC 61131 ofreció varias ventajas significativas en el campo de la automatización industrial. Algunas de estas ventajas incluyen:
- Estandarización: La norma IEC 61131 establece un conjunto común de estándares para la programación de PLCs, lo que facilita la interoperabilidad entre diferentes fabricantes y la reutilización de código en diversos proyectos.
- Variedad de lenguajes: La norma define cinco lenguajes de programación distintos: Lenguaje de Diagrama de Escalera (LD), Lenguaje de Instrucciones (IL), Lenguaje de Programación Estructurado (ST), Lenguaje de Bloques Funcionales (FBD) y Lenguaje de Texto Estructurado (STX). Esto permite a los programadores elegir el lenguaje más adecuado para cada tarea y preferencia personal.
- Flexibilidad: La variedad de lenguajes de programación y la estructura modular de la norma permiten desarrollar programas complejos de manera flexible y escalable, lo que facilita la implementación de sistemas de control más sofisticados.
- Mantenimiento y depuración simplificados: La programación estructurada y modular facilita el mantenimiento y la depuración de los programas, ya que divide el código en bloques más pequeños y manejables, lo que facilita la identificación y corrección de errores.
- Facilidad de aprendizaje: La estructura y los conceptos de programación definidos en la norma IEC 61131 son intuitivos y fáciles de aprender, lo que facilita la capacitación de nuevos programadores y reduce el tiempo necesario para desarrollar competencias en programación de PLCs.
El futuro de la automatización y la Universal Automation
El futuro de la automatización industrial se vislumbra emocionante, con avances en inteligencia artificial, aprendizaje automático y robótica colaborativa. Organizaciones como la Universal Automation Org, están liderando el camino hacia una automatización más inteligente y adaptable, promoviendo estándares abiertos y la interoperabilidad entre sistemas. Con la integración de tecnologías emergentes y una mayor colaboración entre los actores de la industria, se espera que la automatización continúe transformando los procesos industriales y creando nuevas oportunidades de crecimiento y desarrollo.
Conclusión
En JAR queremos crear un mejor futuro para todos a través de la aplicación de la tecnología haciendo uso de los Controladores Lógicos Programables y la automatización industrial, estamos en camino de lograr una mayor eficiencia, productividad y sostenibilidad en la industria. Al adoptar las últimas tecnologías y colaborar en la creación de estándares abiertos, podemos construir un futuro donde la automatización mejore la calidad de vida y promueva un desarrollo económico y social sostenible.
Para más información nos puede contactar en automatizacion@grupojar.com.mx